Innovative 3D Printing Meets Electronics Exploring the Energy Sword, Media Dial, and Milk Crate Projects in 3D Product Visualization
Innovative 3D Printing Meets Electronics Exploring the Energy Sword, Media Dial, and Milk Crate Projects in 3D Product Visualization - 3D Printed Energy Sword Prototype Using Feather PropMaker 2040

The "3D Printed Energy Sword Prototype Using Feather PropMaker 2040" demonstrates a clever blend of modern 3D printing and electronics, resulting in a sizable prop—the blade measures 86 cm in height and tips the scales at roughly 3 pounds. Its core lies within the Feather PropMaker 2040, a microcontroller board incorporating an RP2040 chip alongside an integrated audio amplifier and accelerometer, thus adding interactive capabilities. Constructed from 20 distinct pieces that snap together, the sword's design is open-source, made available through downloadable STL files—users can tailor the model to their liking. The implementation of NeoPixel LEDs enhances the sword's visual impact, providing dynamic lighting effects that are sustained by a rechargeable 2000mAh battery, granting several hours of operation. This particular project is a testament to the creative integration of electronics with 3D-printed designs, which opens new possibilities for crafting functional and visually striking props, perfect for cosplay, displays or even creative product presentations.
This Energy Sword prototype, standing at a notable 86 cm (34 inches) tall and weighing in around 3 pounds, is a compelling example of what's achievable with the Feather PropMaker 2040. This compact development platform, incorporating the RP2040 chip, audio amplifier, and accelerometer, makes the build process surprisingly streamlined. The sword is assembled from about 20 snap-fit pieces – handles, blade sections, and so on – making it a modular design. It incorporates NeoPixel LEDs connected to an Adafruit Feather BLE 32u4, enabling a range of lighting effects that help capture the energy sword's iconic visual character.
Power comes from a 2000mAh LiPo battery, allowing for a few hours of use before requiring a USB charge. It's also encouraging that the project provides free STL files. This allows individuals to modify or tweak the design based on their needs. The sword can be printed using methods like FDM or SLS, offering a degree of flexibility based on available 3D printing resources. It's interesting to see this specific project as part of a larger Adafruit initiative, which includes projects like the Media Dial, showcasing a creative exploration of prop creation through 3D printing.
From a design perspective, the combination of electronics and the 3D-printed parts creates an interesting outcome. The focus is on user experience and the 'wow' factor often associated with cosplay and prop displays. The Energy Sword project, along with similar projects in the Adafruit series, is a clear demonstration of what's possible when merging 3D printing with integrated electronics. You get functional props that are visually compelling, showing that this intersection of technology has a lot of potential in various fields, from hobbyist projects to specialized designs.
Innovative 3D Printing Meets Electronics Exploring the Energy Sword, Media Dial, and Milk Crate Projects in 3D Product Visualization - Snap-fit Design of Energy Sword Blades for Easy Assembly
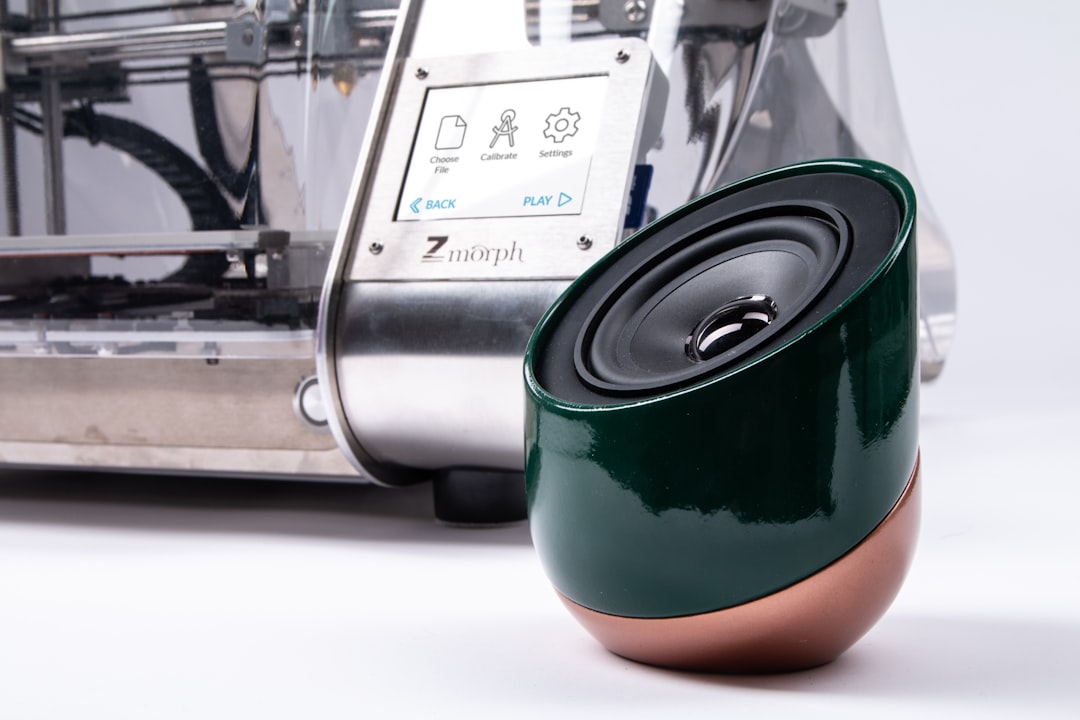
The Energy Sword's blade design cleverly employs a snap-fit approach, breaking down each blade into four segments per side. This modular design significantly streamlines the assembly process, eliminating the need for screws, glue, or other traditional fasteners commonly used with 3D-printed parts. This innovative technique not only simplifies construction but also contributes to a cleaner, more polished aesthetic. It's noteworthy that the success of snap-fit designs hinges on careful planning. Factors like clip width and joint design directly impact the strength and reliability of the assembly. Optimizing these aspects can lead to a more robust and functional product, highlighting the potential of snap-fit technology for enhancing both the assembly and the overall quality of 3D-printed objects. This approach has the added benefit of potentially lowering manufacturing costs, a positive development for hobbyists and creators alike. It is interesting to see how the principles of efficient assembly through snap-fits can be successfully applied to relatively large and complex 3D-printed designs, particularly in projects where visual appeal and ease of construction are desired.
While there are some benefits to this assembly technique, some might see it as more complex for a specific set of users. For example, properly aligning the snap-fit pieces may need careful attention, and an improper fit could compromise the final product's structural integrity. Regardless of this, the choice to leverage a modular snap-fit assembly in a 3D-printed product points towards trends in manufacturing. Overall, it's a good example of how 3D printing technology can be coupled with intelligent design choices to address functional needs and improve assembly methods.
The Energy Sword's design utilizes a clever snap-fit approach for its blade sections, splitting each side into four pieces. This method bypasses the need for traditional fasteners like screws or glue, streamlining the assembly process—especially valuable for 3D-printed components. Interestingly, horizontal printing layers, parallel to the joints, are recommended to bolster the strength of these snap-fits in FDM 3D printing, a common technique.
It's intriguing how snap-fits can potentially cut production costs and improve the overall aesthetics of a product, especially compared to more traditional assembly methods. Achieving strong and stiff joints seems to hinge on optimizing the dimensions of the clips or hooks. A minimum of 5 mm seems to be a rule of thumb for ensuring strength, based on this project.
This approach of utilizing snap-fits goes beyond the Energy Sword and holds potential for wider applications. From designing complex microrobotic systems to creating more intricate sensor assemblies, the concept allows for quick and easy assembly and disassembly of intricate parts. However, it's important to note that achieving successful and reliable snap-fits in 3D printing necessitates thoughtful design decisions. Joint type, the materials used (like FDM or other 3D printing resins), and proper design practices are all critical factors for achieving durable and functional assemblies.
This kind of design can improve production efficiency, cutting down on labor and materials, which can be incredibly important in achieving scalable production numbers. It's a bit of a balancing act though—effective snap-fit designs must carefully consider the interplay between materials and joint geometry to get a robust product. That's where the use of materials like those provided by FDM printing (or potentially SLS printing, depending on the application) in a 3D printing environment comes into play. The choice of material directly influences the end-use performance, durability, and, of course, the effectiveness of the assembly method itself. It's a great illustration of how material science and engineering are interconnected in a design process like this.
Innovative 3D Printing Meets Electronics Exploring the Energy Sword, Media Dial, and Milk Crate Projects in 3D Product Visualization - LED Integration in 3D Printed Electronics Projects
Integrating LEDs into 3D-printed electronic projects is increasingly significant, driving the creation of more interactive and visually appealing products. The use of LEDs allows for new possibilities like flexible OLED displays and enhanced 3D-printed parts, revealing a clear connection between lighting and the 3D printing process. This fusion isn't just about aesthetics; it adds to the functionality of products through applications like energy generation and dynamic visual effects. As 3D printing techniques become more refined, integrating LEDs efficiently and precisely could unlock new design frontiers. The Energy Sword project, for example, demonstrates this potential by using LEDs to enhance its appearance. The combination of 3D printing and LED technology offers a pathway towards a future of innovation within the wider realm of electronics and product design.
While the technology holds promise, challenges remain. Issues like the durability of LEDs within a 3D-printed environment and the energy efficiency of these combined systems will need further development. It also raises questions about how we can best leverage AI and product image generators in ecommerce to showcase the dynamic and interactive nature of products that integrate LEDs and 3D-printed components. Despite these challenges, the overall potential remains immense, leading to interesting new avenues within product design, both in the context of specialized creations and mass-produced goods.
The convergence of 3D printing and LEDs presents a fascinating avenue for creating dynamic and interactive electronic projects. We can see examples of this in projects like the Energy Sword, where NeoPixel LEDs provide vibrant and customizable lighting effects, enhancing the overall appeal and user experience.
However, integrating LEDs into 3D-printed electronics requires careful consideration of thermal management. LEDs, particularly when driven at higher intensities, produce heat. This heat can potentially shorten the lifespan of the LEDs or damage surrounding components. Designers need to actively consider strategies like adding ventilation pathways or incorporating thermally conductive materials into their designs. Otherwise, issues with component overheating might arise.
One of the intriguing possibilities arising from this combination is the use of flexible circuits. Flexible circuitry lets us push the boundaries of design and create electronics that adapt to complex shapes. This could have implications for a whole host of products, like wearables or products with uniquely shaped display panels.
The ability to leverage multi-material 3D printing further broadens the possibilities. With multi-material printers, you can combine conductive materials with more traditional plastics or filaments, creating functional devices where structure and circuitry are essentially printed as one piece. This integrated approach simplifies assembly and can lead to a more reliable product.
A common challenge with LEDs is achieving a consistent and even distribution of light. Employing diffusing materials or techniques within the 3D-printed design itself can make a significant difference. Applying carefully designed surface patterns or incorporating translucent components can help spread the light evenly, avoiding the "hotspot" problem we sometimes see with direct LED illumination.
It's becoming more common to see engineers using CAD software to virtually simulate electrical circuits within their 3D designs. This not only helps to better understand the flow of current but can reduce design iterations during the physical prototyping phase. We can quickly see if LED placement and the general electronic design will function as expected in the digital model before actually printing a prototype and discovering an error.
While LEDs provide a nice visual enhancement to many 3D printing projects, power efficiency also needs consideration. If you're working on projects with limited battery life, choosing specialized microcontrollers that consume very little power can make a big difference in usability. Power management becomes very important when working with these kinds of interactive systems.
In the art world, the combination of LEDs and 3D printing is enabling entirely new forms of interactive artwork. Artists can create dynamic light displays that change based on factors like environmental conditions or even audience interaction. We're moving beyond static art to interactive creations where the 3D-printed structure becomes a canvas for a dynamic display.
The push to create user-centric designs is also noteworthy in this context. Imagine product displays on e-commerce platforms where customers can easily control the integrated lighting effects. This type of interactive control can significantly enhance the presentation and add a degree of customization that makes the customer experience more personal.
Although integrating LEDs adds functionality and aesthetic appeal, we must consider the regulatory environment. Safety standards related to electrical devices and products can sometimes be complex. Designers need to be aware of and comply with these regulations to ensure the product can be safely sold and used by consumers. This is especially important as 3D-printed electronics grow in popularity.
Innovative 3D Printing Meets Electronics Exploring the Energy Sword, Media Dial, and Milk Crate Projects in 3D Product Visualization - MIT's Breakthrough in 3D Printing Magnetic-cored Solenoids
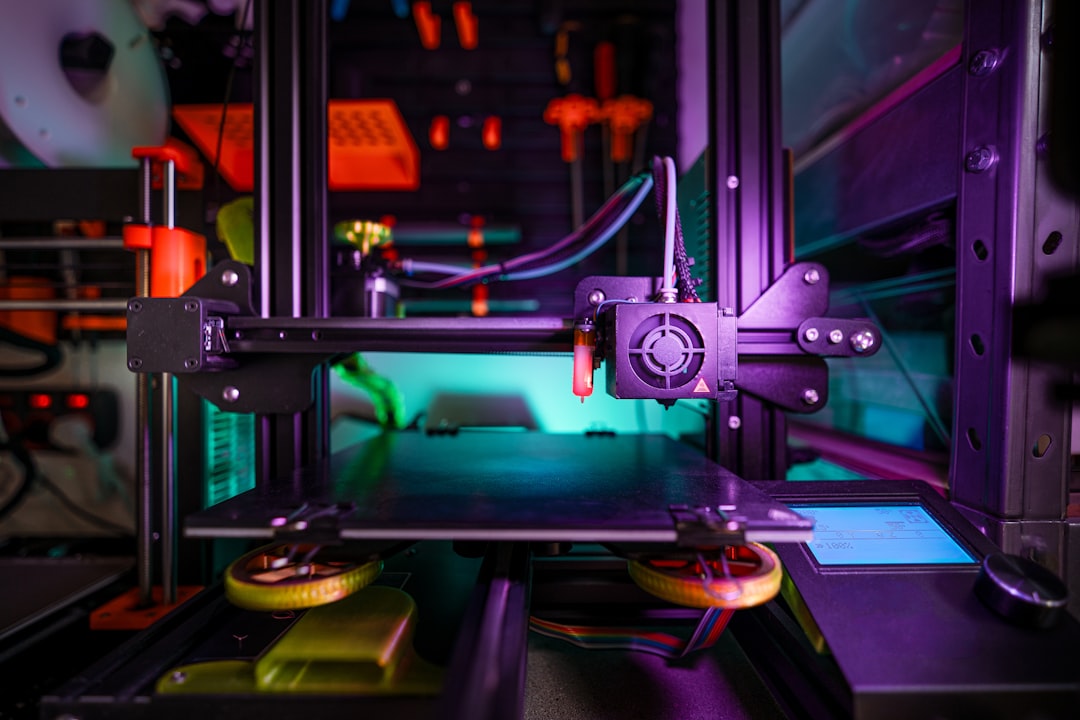
Researchers at MIT have achieved a breakthrough in 3D printing by developing a method to create magnetic-cored solenoids, which are essential components found in numerous electronic devices. Solenoids, essentially electromagnets composed of a coil of wire wrapped around a magnetic core, are used in a wide variety of applications. MIT's team adapted a multi-material 3D printer to produce these solenoids in a single step, leading to compact designs. Notably, these 3D-printed solenoids demonstrate a magnetic field strength roughly three times greater than those currently produced using air-core methods.
This advance simplifies the manufacturing process, eliminating the need for post-assembly procedures that can introduce defects. Consequently, the potential for reduced manufacturing costs is significant, potentially impacting a broad range of electronic products. Furthermore, the ability to directly manufacture complex solenoids in a single step opens up opportunities for in-situ manufacturing within electronic devices. This approach is particularly relevant as the electronics industry actively explores ways to integrate 3D printing with its manufacturing processes. While the research is still in its early stages, it demonstrates a significant step towards more efficient and cost-effective electronics manufacturing.
Researchers at MIT have made a significant advancement in 3D printing by developing a method to create magnetic-cored solenoids. These solenoids, which are essentially electromagnets formed by a coil of wire around a magnetic core, are used in a vast range of electronics, from everyday appliances to sophisticated medical equipment. What's new is that they've figured out how to 3D print the entire solenoid in a single step, doing away with the traditional multi-step assembly process.
The 3D-printed solenoids are designed to incorporate specific magnetic materials that are directly compatible with 3D printing techniques. This allows for better control over the solenoid's final characteristics. A major improvement is the increased magnetic field strength—around three times stronger compared to similar 3D-printed solenoids built with air cores. These devices can generate substantial magnetic fields (in the Gauss range) while drawing relatively little current (tens of milliamps). This makes them well-suited for applications like induction sensors.
One of the major benefits of this method is that the 3D printing process eliminates the need to assemble multiple parts, reducing potential issues like misalignment and other defects that often crop up during traditional manufacturing. This approach could lead to a reduction in production costs, a positive development as the demand for electronic components continues to grow.
This 3D printing technique provides a significant boost to the field of 3D printed electronics. Engineers can now design more sophisticated solenoids for various applications—from advanced robotics to medical technology. Furthermore, this approach could allow for the on-site fabrication of electronic devices. This opens up possibilities for customized electronic systems and manufacturing processes that are closer to the point of use.
It's worth noting that this technology, presented at the PowerMEMS 2022 conference, is still relatively new, but the implications for advanced electronics manufacturing are quite promising. However, we need to consider factors such as managing the heat produced by these solenoids during operation to ensure their long-term reliability. Also, the ability to effectively model and simulate these solenoids in design software, prior to physical printing, is crucial to minimize costly errors. As the technology matures, we might see more widespread adoption of these 3D-printed magnetic cores in many aspects of electronics and other industries. It will be fascinating to see how this innovation further enhances the capabilities of 3D printed electronics and potentially impacts fields like robotics, sensors, and other electronic product designs.
Innovative 3D Printing Meets Electronics Exploring the Energy Sword, Media Dial, and Milk Crate Projects in 3D Product Visualization - DIY Community's Approach to Merging Electronics and 3D Printing
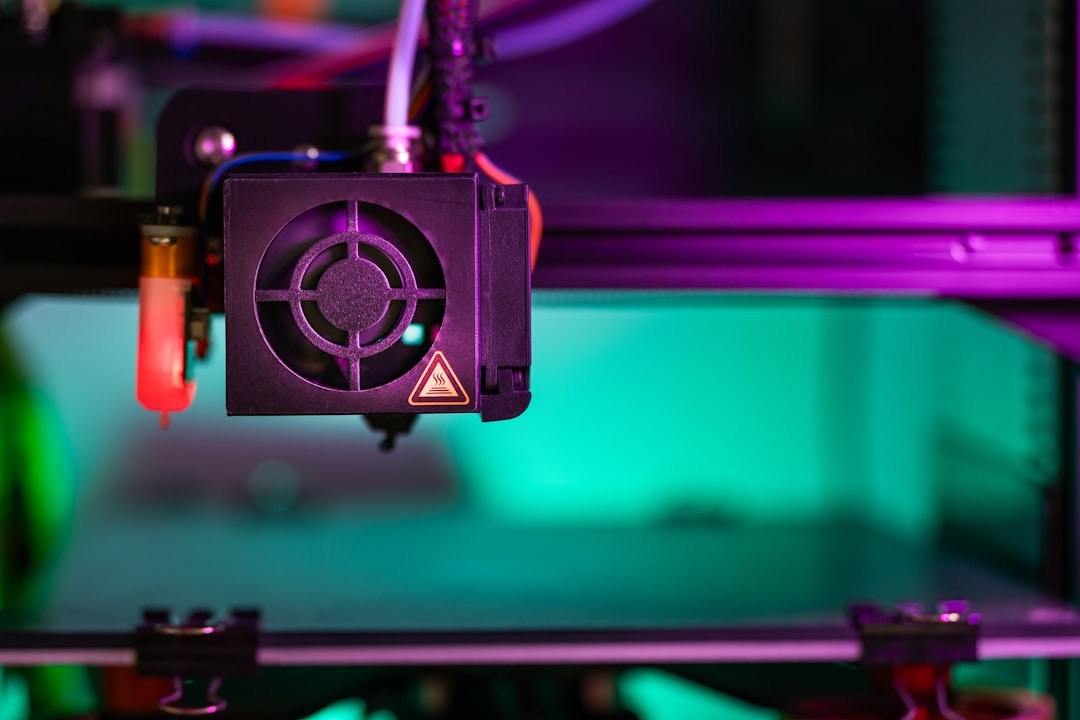
The DIY community is at the forefront of merging electronics and 3D printing, fostering a dynamic and accessible environment for innovation. Projects like the Energy Sword, Media Dial, and Milk Crate showcase how readily available 3D printers empower makers to blend electronic components with intricate, 3D-printed designs. This movement effectively democratizes access to technology while simultaneously encouraging experimentation with new materials and streamlined construction methods, such as modular snap-fit assemblies and LED integration. While there are inherent benefits, the integration also introduces challenges, particularly in maintaining the longevity and operational reliability of these creations. Despite these obstacles, the drive to explore and refine 3D-printed electronics continues to propel this field, blurring the boundaries between traditional crafts and cutting-edge electronics. Ultimately, this combination has the potential to reshape future design approaches, impacting how we create and utilize electronic devices.
The DIY community's approach to combining electronics and 3D printing is fascinating, particularly how they've embraced modularity. Projects like the Energy Sword showcase the ability to swap out components without major design overhauls, making these creations incredibly adaptable. This is largely enabled by the open-source nature of many projects. Sharing designs, like the readily available STL files for the Energy Sword, fosters collaboration and allows for rapid iteration across the community.
One of the key aspects is the synergy between material science and the 3D printing process. Printing conductive materials alongside more traditional plastics creates opportunities for fully integrated electronics directly within a 3D-printed object. This helps make the electronics more reliable and simplifies the manufacturing process. However, integrating electronics introduces new considerations, particularly when it comes to heat. LEDs and microcontrollers generate heat, and without proper ventilation or thermally conductive materials, it can lead to component failures. It's a challenge designers need to carefully manage.
Thankfully, CAD tools are becoming more sophisticated. They're incorporating simulation capabilities that allow engineers to virtually test their electronic designs, which is a big step. They can now predict circuit performance and see if the placement of elements like LEDs will work as intended before a single part is physically printed. This helps minimize errors and the costs associated with redesigning failed prototypes.
Beyond just functionality, these combined technologies are being used to improve user experiences. Projects like the Media Dial aren't just 3D printed shells; they incorporate touch-sensitive elements and interactive lighting. This takes product design to a new level by introducing dynamic and personalized controls, demonstrating the potential for creativity beyond static structures.
Naturally, power efficiency is always a concern when integrating LEDs and other electronic components. Fortunately, low-power microcontrollers are becoming increasingly popular. This is crucial for projects with limited battery life, such as cosplay props. And as resin materials used for 3D printing improve, we see more potential for projects like flexible wearable electronics that are comfortable and durable for users.
However, the integration of electronics also requires careful attention to regulations. As 3D-printed electronic projects become more common, designers need to be aware of and adhere to product safety standards, especially those involving user interactions. This is a growing area of concern that needs careful consideration as the technology matures.
Finally, we can't ignore the impact that visual design has on consumer appeal. The combination of well-designed 3D-printed parts with functional electronics has the potential to create extremely engaging products. This visual impact, crucial for online sales platforms, requires thoughtful product visualization strategies that effectively highlight these exciting features. With thoughtful design and careful consideration of the broader implications, it's a promising direction for future product development.
Innovative 3D Printing Meets Electronics Exploring the Energy Sword, Media Dial, and Milk Crate Projects in 3D Product Visualization - Advancements in UV-curable Inks for 3D Printed Electronics
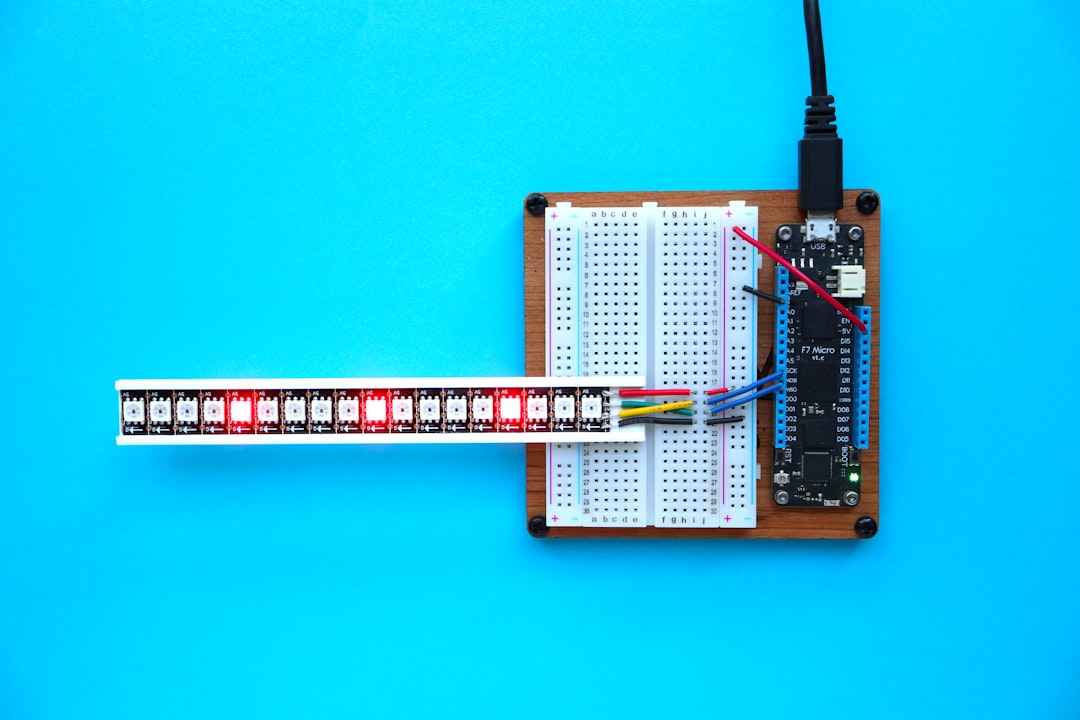
The field of 3D printed electronics is being reshaped by recent advancements in UV-curable inks. These inks allow for a streamlined manufacturing process where multiple materials are jetted and cured simultaneously, which is a more efficient approach than traditional methods. This allows for the inclusion of materials that respond to electromagnetic fields, such as iron oxide nanoparticles, in the printed objects, enabling greater versatility in both the structure and function of 3D-printed products. Another key aspect is the ability to cure the inks during the actual printing process. This has a significant impact on the quality of the final 3D-printed object, both in terms of its precise shape and the overall strength and rigidity of the structure. We're seeing this come to life in projects like the Energy Sword, the Media Dial, and the Milk Crate, which demonstrates that this technology can be applied to creative and practical purposes. However, while this area shows promise, there are still challenges that need to be addressed, such as ensuring the even distribution of tiny particles (nanoparticles) within the ink, which can affect the overall properties of the material and the resulting 3D-printed part. These issues require continued research and development to ensure that these new inks can be used to consistently achieve the desired outcomes.
The field of 3D printed electronics is experiencing a surge in innovation, particularly with the development of UV-curable inks. These inks have evolved to the point where we can now print and cure multiple materials simultaneously in a single step, boosting manufacturing speed. This ability to print and cure on the fly is crucial for producing complex electronic features with precision. The inks themselves are becoming more versatile, capable of offering a wider range of properties. We're seeing inks that are more flexible, harder, or even conductive, which is opening up the possibility of building very complex electronic circuits within the 3D printed structure.
Specifically, the use of conductive UV-curable inks, which often contain silver nanoparticles, is making a big difference. These inks allow for the direct printing of electrical circuits, reducing the need for additional wiring steps. That's a notable simplification of the design process. It also enhances the prospect of creating truly integrated electronics where the functionality is built directly into the structure itself. We can now directly print sensors and actuators during the 3D printing process, making the creation of 'smart' products much easier and more efficient.
Another interesting facet is the increased substrate compatibility. Many of these new ink formulations work with a wide array of materials, including flexible ones. This opens doors to new applications in areas like wearable electronics and other fields where the traditional rigid electronics were a hurdle. The ability to precisely control UV exposure during the printing process also enables the creation of ultra-thin, layered electronic components, which is extremely important when we are dealing with high-performance, space-constrained electronic designs.
Furthermore, the improved mechanical properties of these inks are a significant development. Modern formulations exhibit greater resistance to solvents, heat, and physical wear and tear, which enhances the longevity of these 3D printed electronic products. It's an interesting shift towards sustainability too, as the additive manufacturing approach using UV-curable inks inherently produces less waste compared to traditional manufacturing methods that involve removing material. The need for high-temperature resistance is also being addressed. Researchers are formulating inks that can perform reliably in environments that were previously challenging, again extending the possible uses of 3D printed electronics.
The synergy between UV-curable inks and advanced design software also presents an exciting path forward. This integration allows engineers to simulate and optimize the electronic designs before they are ever printed, which is really valuable for speeding up the design process and minimizing mistakes. While there are always hurdles to overcome, the advancements in UV-curable inks for 3D printing are driving the field forward at a rapid pace. We're not just creating objects; we're developing increasingly complex and functional electronic systems that are 3D printed. The potential for innovation in the design and manufacturing of electronic products is significant, and it's encouraging to see the progress being made.
More Posts from lionvaplus.com: